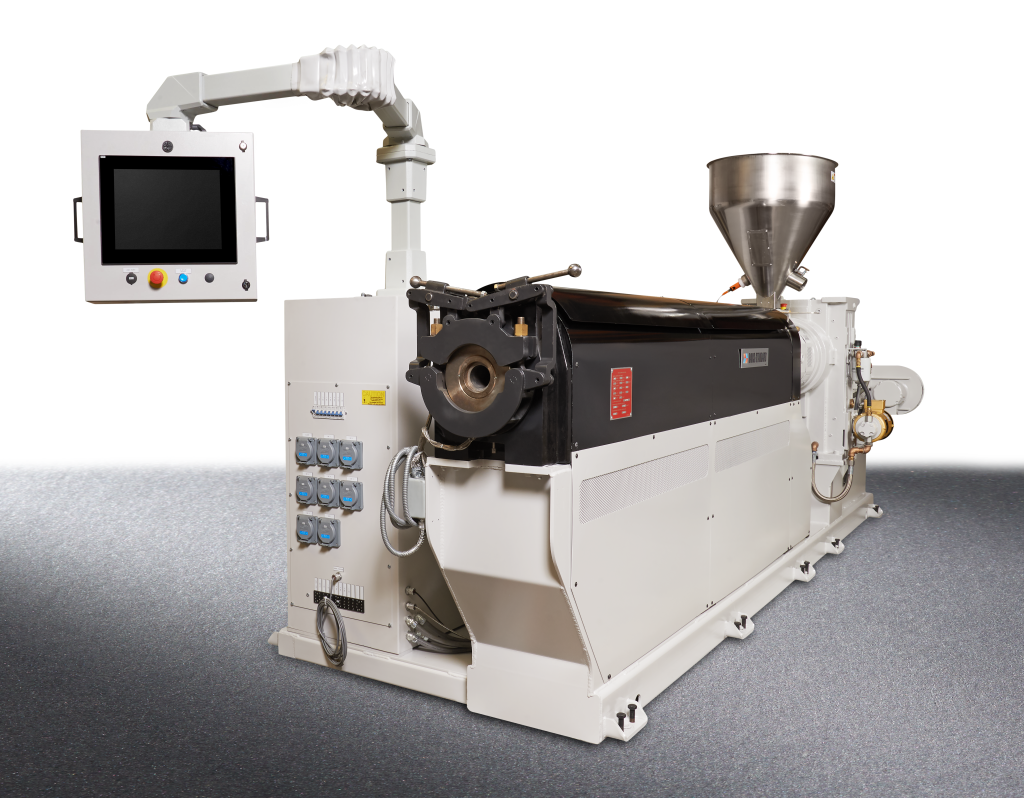
Davis-Standard will exhibit machinery and process solutions that highlight a commitment to value, innovation, and sustainability during the upcoming K2022 Show in Düsseldorf, Germany, Hall 16 Booth A43. Technology from the Davis-Standard family of companies, including Davis-Standard, Maillefer, Brampton Engineering, Deacro and Thermoforming Systems LLC (TSL), will be shown with an emphasis on customer profitability and performance. Visitors will experience continued developments in extrusion and converting technology focused on a circular economy, energy efficiency, reduced power consumption and minimized waste, as well as a live demonstration of smart factory connectivity.
“As the first K show since 2019, we look forward to engaging with our global customer base and sharing new developments,” said Giovanni Spitale, Davis-Standard President and CEO. “Our exhibit will present a range of technology from Davis-Standard and our heritage brands that reflects marketplace demand and our strong commitment to sustainable manufacturing practices. We also have an intense focus on the lifecycle value of our machinery as reflected in our aftermarket services.”
Davis-Standard has been active since the last K show, and is eager to introduce enhancements and developments to its expansive machinery portfolio. Following is a summary of technology to be shown and/or promoted:
Aftermarket Advantages – Davis-Standard and all portfolio brands offer end-to-end service, parts, and line upgrades to help customers maximize productivity. The company continues to push the envelope with smart factory solutions and connected machinery developments designed to integrate with a customer’s plant to provide real-time monitoring and diagnostic capability. For example, Davis-Standard’s new DS Activ-Check™ platform can be installed on a continuously expanding number of company products (including both Davis-Standard and Maillefer machinery), delivering a powerful suite of analytical tools, cloud and local data storage options, process and equipment technology algorithms. A live demonstration of how customers can benefit from this technology will be given during the show.
SHO Extruder (3.5-inch, 90mm) – Equipped to save space while offering outputs of at least 20 percent versus existing groove feed models, the SHO is engineered with a new gearbox, an optimized feed section, and high-performance, energy-efficient DSB® barrier screw. This is especially beneficial for high-viscosity HDPE applications such as pipe extrusion, where lower melt temperatures, reduced power consumption and improved energy efficiency are paramount.
MXD Extruders – Maillefer’s new MXD series high-performance extruders will be on display in 45mm and 80mm sizes. Besides the two extruders will be three ECH extrusion heads dedicated to three application areas; micro-drip irrigation, blown fiber microduct, and heating and plumbing applications. Downstream equipment will also be shown, featuring the most recent dual coiler and reeler technology with robotized handling capabilities.
Model 4000AG Crosshead – In elastomer, Davis-Standard will promote the Model 4000AG crosshead, which allows for faster start-up times and little scrap. The Model 4000AG incorporates an automatic, servo-driven concentricity and wall thickness adjustment system. This new, proprietary and patent pending, system automatically adjusts core tube/tip assembly to minimize eccentricity, maximize concentricity, and reduce downtime during product changeovers. This automated design has a tapered mandrel and highly engineered flow paths to ensure consistent flow through all speed ranges.
Extrusion Die 510A – Engineered for packaging, cup stock, board and paper, foil, and film applications, the 510A offers simplified operation, improved safety and reduced waste. A short die lip facilitates minimal edge bead, excellent cross profile, and needed flexibility for processing various polymers at changing web widths. The motorized deckling adjustment promotes safe operation, and an optional way-encoder reduces waste during product changeover. The corrosion-resistant chrome nitride surface enables a sharper die exit edge to minimize polymer build-up and increase running time.
Extrusion Laminator – A laboratory-style linear three-roll laminator with a 900mm chill roll will be shown. This design is engineered for a high cooling capacity at high-speed operation, and with a hydraulic linear nip pressure system to support a range of flexible packaging substrates. Advantages include a water-cooled hydraulic actuated take-off roll for gap and contact operation; process rolls with a quick release water connection and simplified roll change function; and a motorized Teflon tape system and belt adjustment for safe, uninterrupted operation.
XP Express® AGT – As the latest addition to Davis-Standard’s roll stand portfolio, this model provides greater automation and process control for sheet extrusion applications. With a space-saving, multi-roll design, processors can take advantage of advanced cooling and polishing, die-to-nip management, web flatness, heat transfer, consistent sheet clarity, and improved performance for low melt-strength resins.*
Feedscrew Display – A single screw extrusion plastication model will show the transformation of raw plastic material into melt as it is pushed to the front of the screw through a rotational action. A single-stage metering screw and single-stage barrier screw will also be displayed. These designs illustrate the mixing quality and efficiency of Davis-Standard’s screw technology in conveying, compressing, and blending melted pellets and color additives into a homogeneous melt stream.
Schedule an appointment with us prior to the show so we ensure ample time for your needs! Click here to get your spot today.
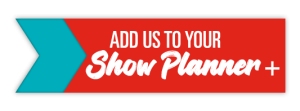
*Disclaimer: This Roll Stand XP Express® – Active Gravity Touch (AGT) is not offered and sold to customers in and from the Federal Republic of Germany at any time in the past and in the future. – Das Walzengerüst XP Express® – Active Gravity Touch (AGT) wird zu keinem Zeitpunkt, weder in der Vergangenheit noch in der Zukunft, einem Kunden in und aus der Bundesrepublik Deutschland angeboten.